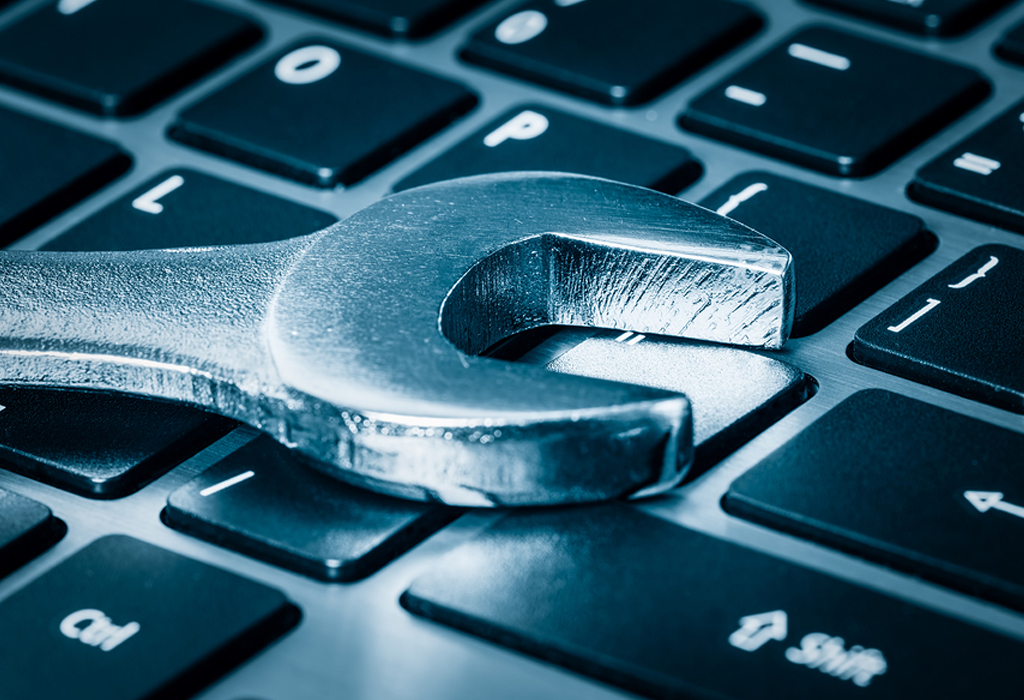
2016 has been a great year for metal fabrication. In 2017 we are hoping the industry continues to build on the innovations and progress made this year, especially when it comes to metal cutting fiber lasers and tools to increase efficiencies and productivity. As 2016 comes to an end we’re looking back on this year’s top tips for metal fabrication shops that we can carry forward – and improve on – in the new year.
Here are the top five tips for fabricators:
Ensure your compressed air is clean, dry, and lubricated
The quality of compressed air is crucial to the reliability of your metal fabrication machines and your shop and business as a whole. You want to set up your lasers, punch presses, press brakes and other machines for success – starting with quality compressed air. Air delivery systems aren’t always perfect and air can pick up impurities throughout the process. Critical to ensuring quality compressed air is the FRL, which filters, regulates and lubricates. A dryer is also a great idea so that clean, dry air is arriving at your machines.
Learn more about why quality compressed air is important and how to make it happen.
Don’t forget about laser maintenance
With all machine tools regular maintenance is key for productivity. This is especially true for laser machines. C02 lasers are complex machines. A quick 1-hour inspection can unveil potential problems such as vacuum leaks, optics quality or cleanliness issues, power output, as well as the maintenance of the turbine and vacuum pump.
Following a maintenance schedule will ensure your machines are performing at optimal levels and can prevent issues that can slow or stop productivity as well as avoiding costly repairs.
Here are few steps you can take to improve machine life and avoid unplanned breakdowns from our guide.
Boost productivity by increasing the speed of machine functions
Slow and steady may have worked for the turtle but when it comes to metal fabrication machines speed is key. Faster machine functions means more parts per hour and more money for fabricators. When it comes to fiber lasers, piercing and cutting times, as well as shuttle table exchange, all make a difference in productivity.
Check out the benefits of increased speed for shuttle tables and the faster piercing speeds of fiber lasers.
Cut operating costs
Boosting productivity and increasing efficiencies are important but they’re even better when you can cut operating costs as well. All three of these factors impact the success of your metal fabrication business. We already love how the enhanced power and speed of fiber lasers decrease processing times but they also cost less to operate. Fabricators are noticing that solid state resonators, on average, cost 50% less to operate than C02.
Automate complicated processes
Many processes in metal fabrication require both a high skill-set and heavy lifting. One of the most complicated processes is the bending process; it’s becoming increasingly difficult to find operators that are skilled and knowledgeable. Moreover, safety and ergonomics further complicate the matter.
We suggest welcoming robots into your shop with open arms! Automating this process with the retrofit solution for press brakes allows you to run a lean team and remove risks associated with the craft.
Learn the four reasons to automate the bending process.
We’re always on the forefront of new technology and innovation to make your fab shop more efficient, productive and profitable. Taking what we know now and implementing and building on it to form new and better processes for the future are key to putting your best interests forward in 2017 and beyond.
Want to schedule a consultation to see how we can help you reach your goals in 2017? Contact us.
Comments
Add Comment