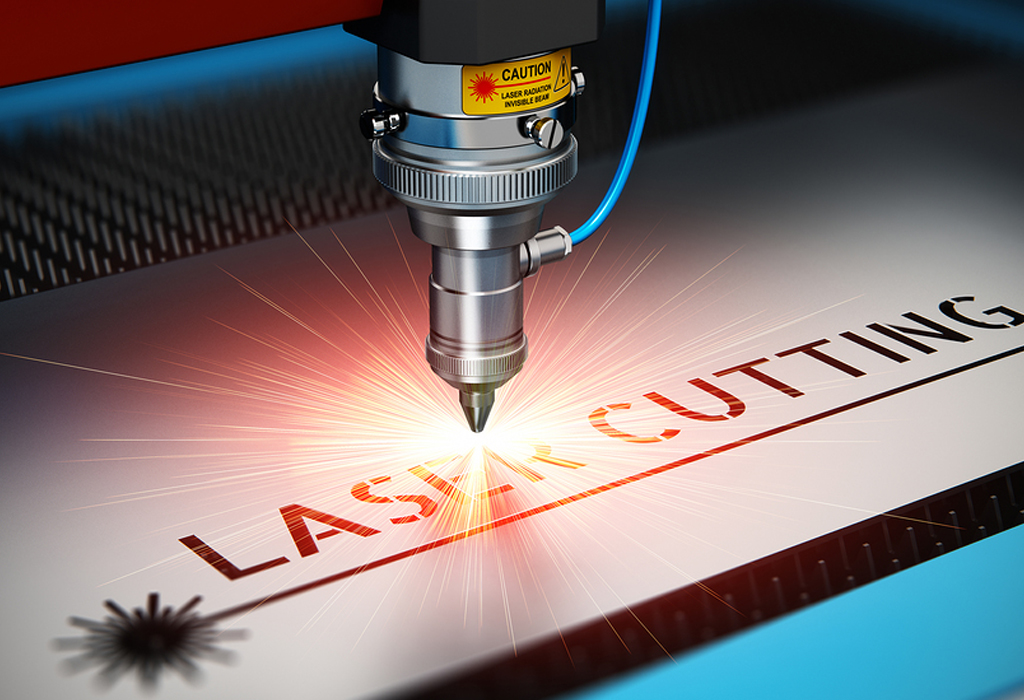
Laser cutting has come a long way, especially when it comes to piercing. It’s the first step; nothing else can happen until the sheet is pierced. Pierce times become critical as the number of holes increase. As fabricators we’re always trying to maximize the capabilities of our shops. That’s where fiber lasers come in. Fiber lasers cut down on processing time with faster piercing and cutting speeds and increase efficiency with lower operating costs.
Need for speed
The cutting process relies on the first pierce; you can’t cut a sheet until the beam is through. Speed is the key here; the faster you can pierce the sheet, the faster everything else in the process goes.
With fiber lasers speed comes from power. As more power is focused into the beam it cuts through material faster. Relatively small increases in power can see much bigger increases in speed. However, the power increase doesn’t necessarily result in equivalent speed increase, for example, 50% more power won’t equal 50% faster cutting. That said, more power always translates in to faster cutting.
Laser sharp accuracy
Precision is another benefit of fiber lasers. Industry experts have noted the advanced capabilities of fiber lasers, including their ability to perform more complicated piercing routines with multiple frequencies and power settings, offset height adjustments and automatic modification of the beam focus, even while the machine is cutting.
With fiber lasers fabricators have greater control over the beam for smaller, more precise holes. Not only can fiber lasers cut faster they do it with more accuracy for less risk and fewer operator interruptions, and a better final product.
Not all materials are created equal
Today’s Fiber lasers cut all materials with greater speed and accuracy than their predecessors, including CO2 lasers. While they will cut down on processing time not all material thickness will reap the same rewards.
Fabricators processing thin materials have the most to gain from fiber lasers as they will see the most significant increase in piercing speed. Fabricators consistently processing thicker materials will still see a difference, but not as radical, as demonstrated in the chart below.
Cutting time, increasing efficiencies
Time is not just hands on a clock for fabricators; time dictates the shop’s bottom line. More power equals more speed, which translates to more parts per hour. Switching to a fiber laser is almost synonymous with productivity enhancement, allowing your team to deliver results faster. The ability to create more parts per hour helps to justify the upfront cost of updating your machinery.
More parts per hour make for increased profits and happy fabricators. In a metal fabrication shop it’s always good to make your seconds count. With a fiber laser you’ll be counting all the more parts at the end of the day.
Piercing Time Reduction on 10mm Carbon Steel
Piercing Time Reduction on 15mm Carbon Steel
Piercing Time Reduction on 20mm Carbon Steel
Comments
Add Comment