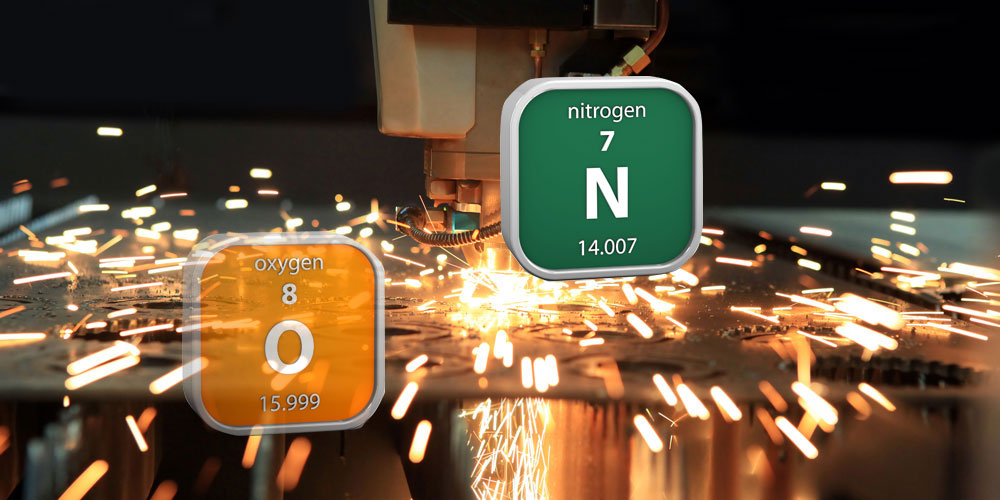
All laser cutting processes for metal fabrication require the use of an assist gas. Depending on material and application, the assist gas may be active or inert (non-reactive). The two most common assist gases are nitrogen and oxygen. While they have things in common, they are very different gases that produce different results. But how do you know whether to choose nitrogen or oxygen for your laser cutting?
We’ll break down the differences between using nitrogen or oxygen as your assist gas and where they are best used. But first, let’s start with the basics: what is assist gas and why do we need it for laser cutting?
Why do we need assist gas in laser cutting?
Regardless of machine type or class, you need an assist gas for laser cutting. The main purpose of assist gas is to shield the laser beam from regular atmospheric air and blow away molten material.
Both nitrogen and oxygen have two main things in common:
- By blasting these gases at high velocity, you blow away the metal that has been melted by the laser, leaving a cleaner cut.
- Both gases also act to remove heat from the metal sheet, minimizing the area affected.
When deciding between nitrogen and oxygen, it’s their core differences that set them apart.
Nitrogen vs oxygen for laser cutting
The main difference between these two assist gases is their classification. Nitrogen is inert (or non-reactive) and oxygen is reactive.
Many fabricators wonder what assist gas is better for laser cutting, nitrogen or oxygen?
The answer: it depends on the application.
Certain applications require non-reactive gases, like nitrogen, as the assist gas. By excluding oxygen in the cut path, pressurized nitrogen prevents oxidation or material discolouration. It also produces a clean edge, reducing dross by clearing the kerf. Cutting with inert gases is also known as clean cutting or high-pressure cutting.
In contrast, you’d choose oxygen for its reaction with metal that adds to the cutting process. The chemical reaction of metal grabbing oxygen atoms at high temperatures causes an exothermic reaction. That means more heat is produced, which speeds up the cutting process.
The downside with using oxygen is the oxidation of the cut edge. If you need to paint or weld the piece, additional clean up is required before the final product is ready.
How to pick the right gas for your job
There are a few things to consider when choosing an assist gas for laser cutting, including: material, cut speed and cut quality required.
Typically, you’d pick nitrogen as your assist gas for jobs where you need a high-quality cut with clean edges. Common materials to use nitrogen with include stainless steel, aluminum and its alloys. You can learn more about nitrogen’s role in laser cutting here
Oxygen is a common assist gas for carbon steels. Oxygen is also used when cutting thick steel plates with lower wattage machines. The extra heat created allows for cutting thicker material, though the cut speed will decrease. For higher wattage Fiber Lasers, you can use nitrogen to cut even thicker materials at a faster cut speed. With higher power, there is less need for an accelerant like oxygen.
High quality makes the cut
Whether you use oxygen or nitrogen as your assist gas, you’ll want to ensure high purity for best results. For oxygen, look for at least 99.7% purity. For nitrogen, 99.999% purity is ideal.
In laser cutting, picking the right assist gas can be critical to your process and final product. Which will you choose?
Comments
Add Comment