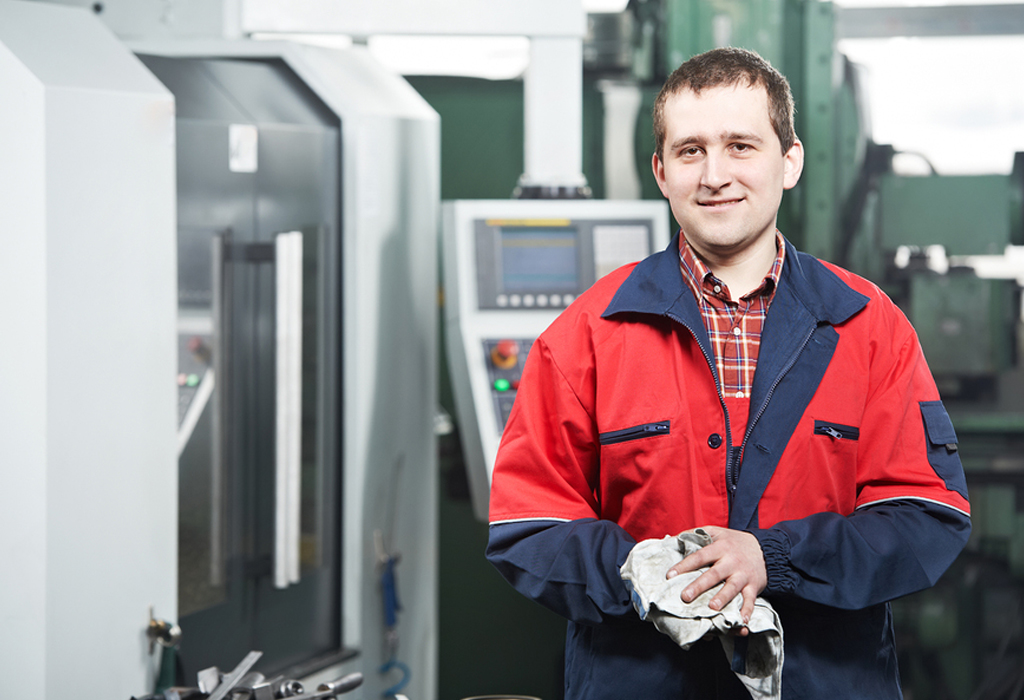
One of the biggest metal fabrication shop ‘hacks’ for productivity is cross-training employees. I’ve said it before and I’ll say it again: investing in your team is investing in your shop. Capitalizing on fewer, well-rounded employees with upgraded skills saves you time and money.
Having a dedicated operator for each machine means that if you lose one (say, someone calls in sick), your shop’s productivity significantly decreases for that day. Likewise, if one machine isn’t running one day, that dedicated employee is stuck twiddling his thumbs with nothing to do – and costing your business.
Developing your employees’ skills not only helps increase their shop knowledge, efficiency and quality of work; it will keep them stimulated and challenged – a big deal when it comes to employee retention. All of these things help keep your costs down and productivity up.
Here are the 3 T’s to keep in mind when cross-training employees:
Training
Whether it’s upgrading your employee’s skills to match upgraded fabrication machines, doing a refresher course on machine shop safety or teaching a new skill, training is essential in any shop. Upgrading your employee’s proficiencies is much like teaching a hungry man to fish: the whole shop (family) benefits.
Teaching your punch brake operator to run the turret is a skill that they can take with them for years, and between shops (if need be). There are three ways to do this:
1) Formal operations training from the machine manufacturer
Manufacturer training ensures you learn exactly what you need to know – but you may potentially need to schedule training from several manufacturers to cover all your bases in the shop.
2) Internal training
Having a well-versed and experienced team member share their expertise with a colleague can be very cost-effective for some shops, provided they are knowledgeable and articulate enough to effectively train an employee.
3) Third-party trainer
For many shops, hiring a third-party company to train employees is a great option. By hiring a technician who is not only proficient with all the machines in your shop, but also a professional trainer, you know all your employees will learn everything they need to know about the proper operation and maintenance of equipment in the best-possible and most efficient way. Click here to find out more.
Time
Just like machine maintenance, you need to allocate dedicated time for training. Even the best-oiled machine won’t matter if there’s no one there to run it properly. The amount of time and frequency for training and skills upgrading will depend on the size of your shop and team, and the types of jobs you work on. When it gets unexpectedly busy, training sessions may be the first thing to rain check. But, scheduling time for training (and making it a priority!) is important – especially when it gets unexpectedly chaotic because your shop’s only press brake operator calls in sick!
Tools
No matter the level of skill, every operator needs basic, good quality tools to get the job done. This can mean upgrading your machinery or simply having functioning measuring instruments on hand.
Keep in mind your employees don’t need a lot of special, costly equipment, just whatever they need ready, handy, and fully functional to do their job. This should be monitored on a monthly basis to keep productivity (and employee happiness) at peak capacity. A great way to keep track is by staying organized and having them fill out a checklist every month.
Especially when it comes to small shops, too many cooks can spoil the broth. Through cross-training you can hire fewer, highly skilled employees to run all of your machines and seamlessly move them around the shop depending on the jobs that need to be done. You may have spent a little bit more time on their skills, but what you’re really spending time on is making your shop run tighter and more efficiently. At the end of the day, your team works smarter, not harder.
Comments
Add Comment