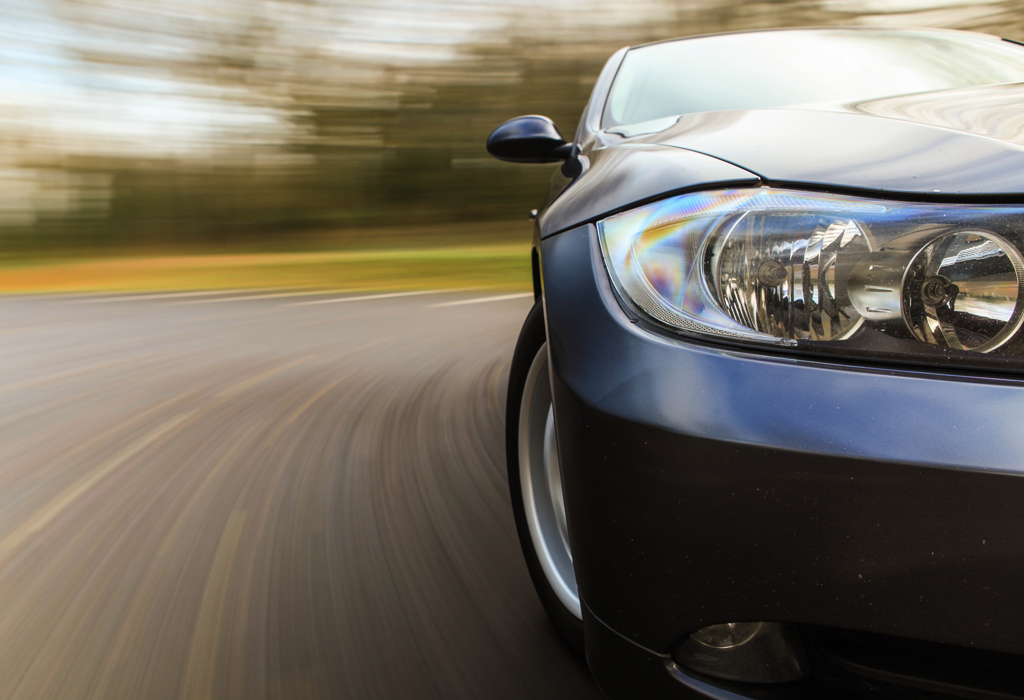
Optimizing the power of fiber lasers: Best practices to keep up productivity of your machines
Advancements in high-power fiber lasers and automation have significantly increased productivity in modern metal fabrication. With the huge number of downstream processes fiber lasers can feed, fabricators need fewer cutting machines to produce more parts – even to the point of replacing several CO2 machines with a single fiber laser.
But, there are some instances that can compromise the efficiency of these machines: if the parts produced are bad and need to be recut, and if the machine crashes and requires downtime for maintenance. Both of these situations can seriously impact the production schedule. Luckily, they can both be avoided by following a few, simple best practices to keep your fiber lasers at their best.
Machine settings are set for a reason
Positioning the beam focus for your material is critical for producing clean cuts. Unlike CO2 lasers, for most materials, a fiber laser beam cutting with nitrogen can focus almost anywhere in the material thickness. While the best focus is often near the middle of the material it can be positioned near the surface middle or bottom and the beam will keep the cut. However, that doesn’t mean that cut will be ideal. With some materials fibers lasers may have a narrow optimal focus window and going outside of it can cause edge quality to degrade and cause dross.
The great thing about fiber laser technology is that most of the cutting conditions are built into the machine. It’s important to keep that in mind. Machine manufacturers have mapped out focal points for various material grades, in some cases even mapping two optimal focal points with a high and a low focus. These results have already been entered into a machine’s factory settings – there is no need to adjust the focus in most cases. So, how do you keep the focus optimal for cuts with great edges? Avoid adjusting factory cut conditions. You might even have material quality issue if your cut quality has deteriorated suddenly.
Same thing with the nozzle gap (the space between the nozzle orifice and the sheet surface). Factory settings typically set this from 0.030 in to 0.060 in, with rare cases going slightly higher or lower. Changing the nozzle gap means changing the amount of assist gas to make a clean cut, therefore changing the gas dynamics for the whole process and impacting cutting consistency.
Speed settings are also set for a reason. On certain fiber laser machines faster speeds can produce better cut edges on thinner materials while for thick materials optimal speeds will be slower.
In addition to reliability, fiber lasers are known for precision. With extensive testing and establishing factory settings, manufacturers have really amped up the precision – making fiber lasers not only more productive and efficient, but easier to use. Remember: the machine manufacturer has spent a great deal of time testing and studying cut conditions and have worked hard to find optimal settings. Changing them can cause edge quality to suffer.
Cover Glass Maintenance
In comparison with CO2 lasers fiber lasers are known and revered for their low maintenance. You no longer need to worry about mirrors and gas resonators, just keep the machine, chiller and dust collector clean. Even the tiniest of spots on the cover glass can cause cut quality to degrade. Now, modern fiber lasers use lateral air jets during piercing and beam parameters are often set so that molten material bursts out sideways and not up into the cover glass. One of the reasons fiber lasers can process greater volumes is the fast piercing speed in addition to cutting speed. But, the piercing cycle is susceptible to blowback. This makes manipulating the beam and the side jet so important during the pierce cycle.
Not all materials are created equal
Quality material is important if you want quality cuts. Materials with imperfections can cause issues when the beam hits the plate surface and can change the assist gas flow dynamic, changing the way the laser cuts. Always consider the materials from the start. Smoother plates allow for more consistent laser cutting.
Programming and nesting
On top of the machine set up and material surfaces, proper programming and nesting are critical to ensuring optimal edges and overall quality. Let’s start with microtabs – necessary for many applications to ensure parts stay in place after they’re cut. Tab placement depends on part geometry. Proper tabbing must both keep the part in place to ensure reliable and consistent cutting and consider downstream processing.
Tabbing also plays a role for pieces susceptible to bowing. With long, narrow parts internal stresses can cause them to bow creating the potential for a head crash. To avoid bowing, place tabs strategically where the most heat deflection is likely. This will hold the parts in place throughout the cutting cycle. Extremely tight nesting, in combination with improper tabbing, can cause issues during the cutting cycle. Strategic tabbing can help prevent interference caused by wobbling and even prevent crashes.
Simple things can make a big impact on the output of fiber lasers. Fiber lasers have seen incredible advancements over the years making them faster, powerful and super precise. They’re also much easier to run with less maintenance. To get the most out of them ensure the basic (and simple) maintenance is followed – but when productivity can be as high as we’ve seen with fiber lasers, keeping a few best practices in mind is worth it.
Comments
Add Comment