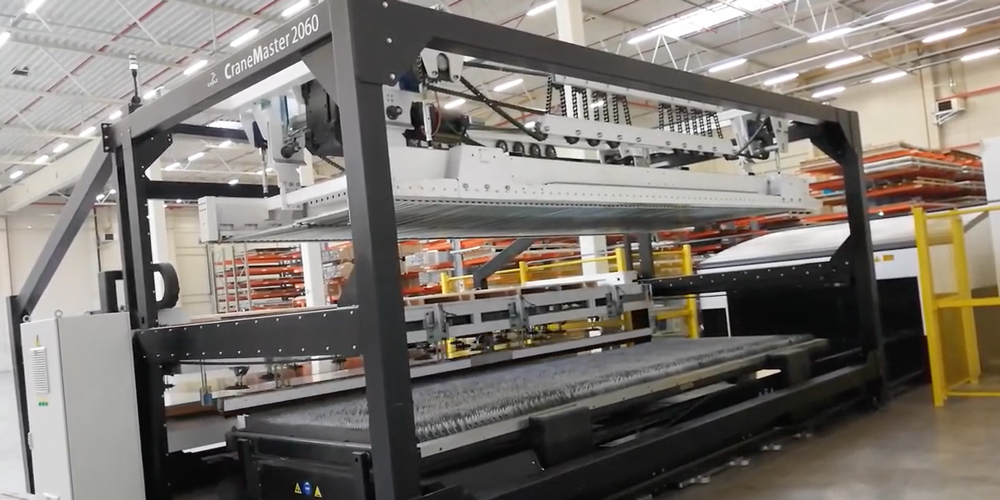
The landscape is competitive in today’s manufacturing world. Demand may be up, but material costs are at an all-time high and the skilled labour shortage means the worker pool is more of a puddle. Fabricators are looking to automation to boost productivity while reducing costs.
While automation may be a new concept for your shop, it doesn’t need to be overwhelming. Integrating automation for labour-intensive, low-skill tasks like part handling can increase output while allowing operators to focus on more valuable work. Thinking about bringing automation to your metal fabrication shop? Here’s what you need to know before getting started.
Have a Vision
Before jumping into automation, nail down your vision to help you determine how you move forward. Think about your team, labour costs and skill sets, the types of work and materials you process, and how time is being spent on the floor. Set a baseline and think about your goals and expectations. Do a full audit of your machine operations and consider how you want to grow your business. You need to have a full view of where you are and where you want to go before you can build the automation system to get you there.
Plan, Plan, Plan
Once you have your vision set, put a plan in place to ensure your success. Plan for the upfront investment, but also for the labour changes, training, and ramp up time. Plus, anticipate your material, tools and fixture needs in advance to avoid leaving machines idle. Ensure you have the right procedures and materials in place so the machine can do its job.
There’s no point bringing in systems to increase productivity if you don’t have the means, materials, or upfront processes to make it happen.
Change Management is Critical
We think about how automation systems can positively impact the business – it can streamline repetitive processes, reduce safety concerns, risk of injury, and more, while boosting productivity. But we often overlook how a change like this can affect the team.
Organizational buy-in is critical when bringing in new technology, as many people need to be involved. The most important aspect of implementing automation is having a team that is excited about embracing new technology and change. You can only integrate new technology successfully if you have the team to do it. To make that happen, you need to be intentional about change management. For many shops, that requires a culture shift – and it’s not always easy.
We are all human. With any change, it is natural that your team may have apprehensions. It is common for the fear factor to come into play, especially with the thought of automation eliminating jobs. Effective communication, training, and education are key to smoothing tension and avoiding resistance. Approach with caution, avoid any friction on the team and encourage positive acceptance by:
- Communicating why it is needed and the opportunity it allows
- Being transparent about how it will affect the workflow
- Providing ample training
- Allowing time for the team to learn about the technology, what it needs to run properly and any potential problems
Strong communication and empowerment can give your team a vested interest in the success of the technology and set you up for the best possible outcome. From increasing efficiency and reducing labour costs, to boosting productivity, employee retention, safety and stability; when everyone is on board, the opportunity is huge. With the right vision, plan and change management, the whole team can benefit from integrating automation.
Comments
Add Comment