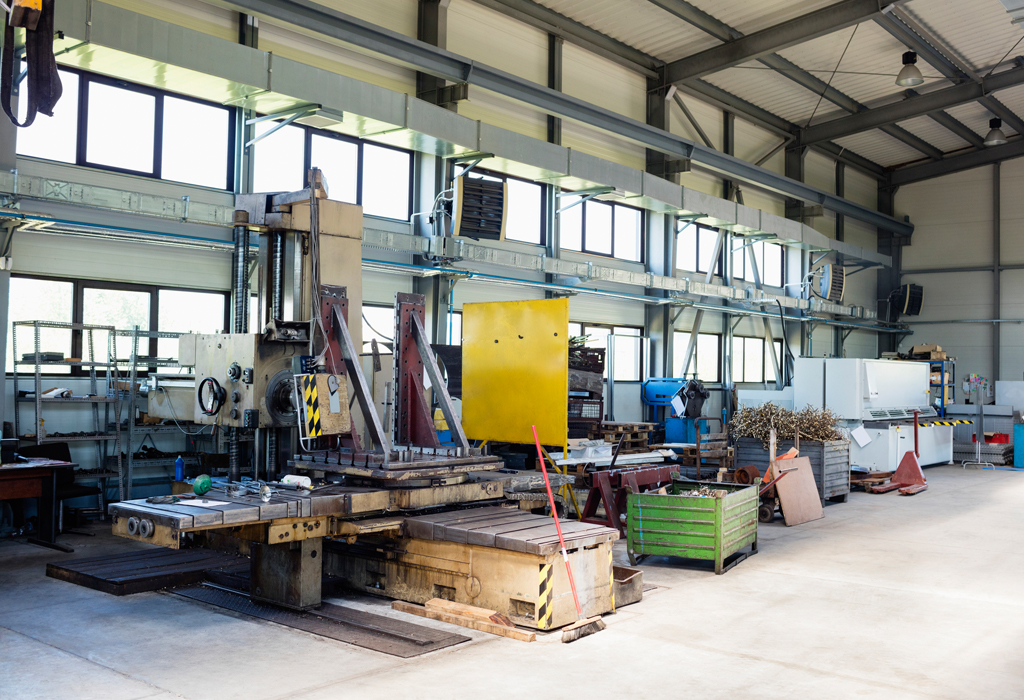
It’s pretty well a law of nature that nothing lasts without proper upkeep. Take the human body, for instance. We all know the often deadly consequences of an unhealthy lifestyle, poor diet and lack of exercise. On a less dramatic note, just think of your car. Don’t you have the oil changed regularly? Have the brakes checked, and regular tune-ups and tire changes?
It’s exactly the same with your machine tools. Any machine will ultimately break down or fail without proper maintenance. Regular preventative maintenance will help prevent problems from occurring while also detecting any problems in their early stages. This will ensure your company averts extensive and expensive damage to your machine tools.
Preventative maintenance extends the life of your machine>
All business owners want to protect their machine investment. It’s therefore of utmost importance to ensure your company implements regularly scheduled preventative maintenance for your equipment. Companies that have a preventative maintenance program in place for their machine tools state that it reduces failures, breakdowns and stoppages.
The ongoing care and cleaning of your machinery will therefore prevent breakdowns and potential failure. You can dramatically extend the life of your machine tools by detecting problems before any major damage can occur. Who wouldn’t want to keep their machines in tiptop working condition to ensure premium productivity?
Why wouldn’t you schedule regular machine maintenance?
Fearing machine downtime and subsequent loss of business, some machine shops cut corners when it comes to scheduling regular maintenance practices. They may baulk at the thought of taking their machine out of production and losing precious time and money, but this is false economy.
A machine that is not properly cleaned and maintained will inevitably breakdown. You can pretty much count on it happening at the worst possible time too! Even more seriously, your machine could fail altogether, resulting in chaos and a very expensive replacement scenario.
Do the math
Keep in mind that almost without exception, component failure is always more expensive than a properly executed maintenance schedule. More importantly, you can schedule preventive maintenance on your own terms at the most convenient times for your company. You can then avoid unplanned downtime, and make machine tool maintenance work and costs more manageable and more predictable. In fact, many companies report that preventative maintenance practices reduce their overall production costs. Most crucial to your business, you will be able to keep your equipment running at peak performance.
While there may be times when you need to replace a part over the life of your machine, this will be part of your designated maintenance budget and not an unplanned expenditure.
Maintenance made simple
Successful companies know the value of regularly scheduled preventative maintenance and also the proper type of maintenance and when to perform it to ensure the longevity of their machine tools. The importance of routine cleaning, lubrication, and inspection cannot be stressed enough.
All machine tools will have a maintenance schedule recommended by the OEM. Owners must assess every machine separately as each machine is different. Usually the manufacturer will call for a variety of preventative measures to be performed at regular intervals, some to be done daily, weekly, monthly and annually.
Good ROI
Machine tool owners who implement a comprehensive maintenance program at their companies report that they significantly improve their machine safety, productivity and cost-efficiency.
The key takeaway for businesses is that regularly scheduled preventative maintenance of your machine tools makes good business sense. Being meticulous about the care of your equipment will pay your company dividends in the long run. A properly maintained machine will last longer, retain its value over the long-term, and provide a good ROI for your business.
Comments
Add Comment