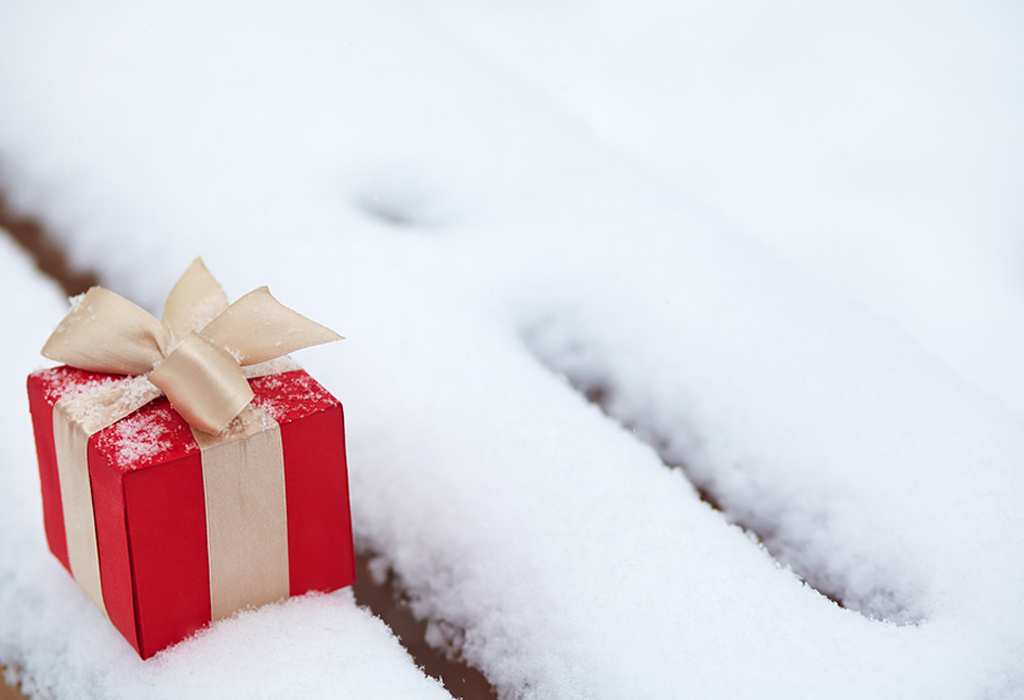
The holiday season is a great time to reflect on the past year and look forward to the next, with eyes for a bigger and better year. Many fabricators are wrapping up this year’s projects and thinking about new opportunities that lie ahead in the new year. But, ‘tis also the season for giving and the age-old question: what do you give a shop that has it all.
To help you make your list (and check it twice), here are 8 things every metal fabrication shop needs this year:
-
Preventative Maintenance
The cost of regular maintenance is a small price to pay to avoid a machine breakdown. Whether it’s taking care of your body with healthy diet and exercise, or getting regular maintenance on your car, preventative action helps you get where you need to go in the long run. It’s the same with machines - it keeps them running longer, avoids downtime and can increase productivity.
-
Oil Change for Hydraulic Machines
People often overlook this step, but the end of the year is a great time for an oil change for your hydraulic machine since many shops shut down. While they have a much larger volume of oil (100-250L), just like your car, changing the oil in a hydraulic machine is critical to keeping it running smoothly – like a well-oiled machine.
-
Cross-trained Operators
What better present than an investment in your team. Your staff doesn’t need to do it all, but the benefits of cross-training your workers are two-fold. Developing your employees’ skills by training them on different equipment or processes helps increase their shop knowledge and efficiency. You can run a tighter ship with staff working smarter, not harder. It will also keep them interested and challenged. Win-win.
-
The right software
IT is often overlooked, but is a big piece of the puzzle for fabricators. The right CAD/CAM software can do wonders for your shop by increasing efficiency and productivity – it is what’s running your machine, after all. A big rule of thumb is to make sure applications are current; outdated software doesn’t always work and can be costing you, especially if it’s only good for one machine. Just as we emphasize cross-training employees above, software that does double (or triple)-duty is also important. There are software packages, including new products by AlmaCAM, to single-source programming of all your machines. This also means you won’t have to deal with multiple supplier and support entities or pay numerous maintenance fees for the various programs.
-
Establishing credit for business expansion
The only way to the top is to go up. Reaching your business goals this year might mean expanding, and that can cause concerns for some – especially those who know more about fabrication than finances. Look to a professional to evaluate your business credit and advise on ways to finance equipment purchase.
-
Machine Inspection
Like a yearly medical checkup, you hope the doctor doesn’t find anything, but if she does, you hope she catches it in time to prescribe a remedy. Regular machine inspection is low risk, high reward. You never know if you might find a critical problem in your machine that could cost weeks of downtime if left unfixed.
-
Automation
Automation is being used more and more in manufacturing today. Its advantages are no secret: robots reduce overhead costs by decreasing the need for staff, and increase productivity – especially for high volume production. It also provides the added bonuses of consistency, reliability and accuracy. But automated bending can be expensive. Get the best of both worlds by retrofitting a robot to an existing press brake. Learn more about Press Brake Robots.
-
Machinery Upgrade
Many machine shops function with out-of-date machinery, but that could be costing them more! Costly repairs, breakdowns, slower processing speeds and quality issues are all problems that can come up with outdated machines. Purchasing quality used fabrication machines that are less than 10 years old is one solution. If you have the budget buying new or even refurbished fabrication machines will offer you new technology along with increased productivity.
Naughty or nice, every machine shop deserves the best. By giving a little, you may get a lot – small changes like these 8 can mean big rewards for fabricators and set you up for your best year yet.
Comments
Add Comment