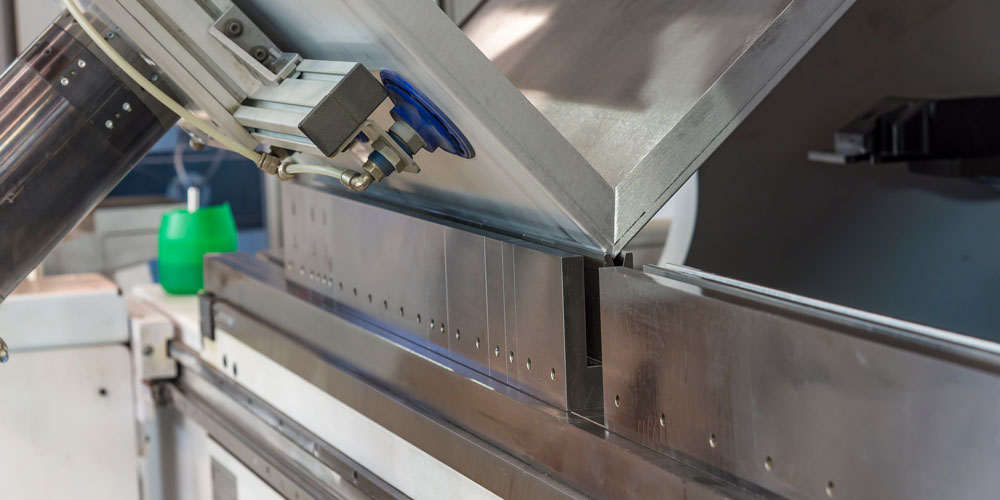
Machine acquisition is undoubtedly a significant investment for all fabrication shops. Often overlooked, equipment maintenance offers a great competitive advantage in all capital-intensive businesses. Adhering to a proper maintenance workflow in your metal shop is vital for achieving the highest efficiency, long life and bottom line improvement. While prompt equipment maintenance ensures maintaining functionality and breakdown reduction, it also reduces the potential for injuries and even fatalities that are critical for the safety of employees.
Most shops know the obvious benefits but not many realize that a well designed equipment maintenance program can play a crucial role in three core elements of competitiveness:
Quality Product Output
Machines that are well maintained are more tolerant and help reduce scrap, thus maintaining consistency and improving quality. Worn-down equipment is likely to manufacture parts or products with unacceptable quality. A predictive and preventive maintenance strategy instead of reactive maintenance takes care of equipment performance and machine wear, ensuring high quality products and customer satisfaction.
Higher Machine ROI
Equipment maintenance helps to increase uptime and yields of good parts. This helps reduce breakdown costs, the need for expensive parts and service, and eventually cuts production costs. Timely maintenance also ensures that machines save on energy consumption and operating cost. Scheduled maintenance goes a long way to extending the lifespan of a machine offering good ROI and longer periods between replacement.
Product Lead Time
Lead time is an essential key metric across many industries. It is an important factor for customer satisfaction. Lead Time also has a direct relationship with inventory at different points in the overall supply chain. Equipment maintenance strategy reduces or ideally eliminates unplanned downtime and the need for retooling. This leads to a shortening lead time. In addition, preventive maintenance allows scheduling procedures according to the facility's and staff's convenience, leading to minimum disruptions in production.
In metal fabricating operations, scheduled downtime for maintenance helps maximize machine availability, reduces costly spare parts, and also service time. Manufacturers of fabrication machines provide recommended schedules for maintenance, which when followed achieve maximum performance.
Managing the Success of Maintenance Programs
To maximize equipment effectiveness production shops need to implement a complete system of maintenance programs that cover the entire life of equipment. It is also important for all departments connected to be involved for the success of the program. Finally, educating the technicians and employees on the importance of machine maintenance through workshops and regular communication ensures proper implementation of routine checkups and daily machine inspections.
Comments
Add Comment