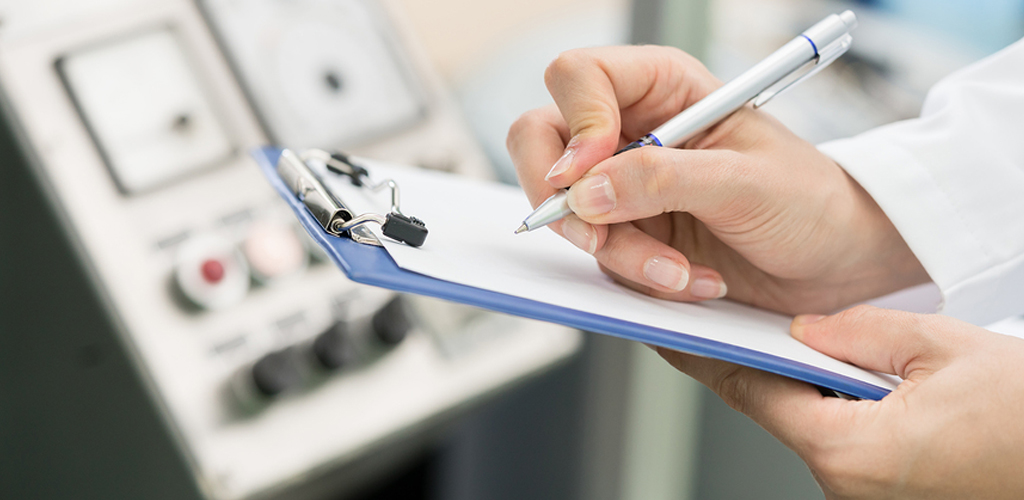
Resource planning tips for an efficiently run fab shop
It’s no secret that preventative maintenance is important for any metal shop. Regular maintenance helps improve machine life, long-term value, safety and productivity, while also preventing problems and detecting potential issues early on. You know the ROI on regular maintenance is huge: it is time and cost-effective, and can save your business in the long-run.
But not just any maintenance will do; you need a plan. A well-thought-out regular maintenance process is crucial for maintaining your fabrication machines in the most cost-effective and successful way. Asset auditing is the first and most important step for creating your plan.
Here are three crucial components to asset auditing and why they’re important for your metal fabrication business:
Assess your machine inventory
A good machine inspection is the starting point for any asset auditing process. You’ll want to get a full picture of the condition of the equipment you have, to make decisions for the future. Take detailed notes on every aspect of your equipment, including location on the shop floor, condition, use, age, life expectancy, and any other relevant information.
At Paramount Machinery Inc., we have our own standardized, thorough checklists geared specifically to each type of machine – punch press to fiber laser, and more. As experts in many kinds of metal fabrication machinery, we know exactly what to look for and can make accurate conclusions to help you decide your next course of action. An inspection takes approximately two to three hours.
Audit your equipment
Once the inspection is complete, you will have a clear idea of where you stand with your equipment, what service it needs and the costs it will entail. After every inspection we do, we make suggestions on how to best use and maintain your machines.
One of the biggest question to consider before you decide on your next steps is how much effort a piece of equipment will take to maintain. You’ll also want to think about your company goals – do you have enough equipment, or the right equipment, to meet your quotas? Do you have extra or unnecessary, unused machines, that you might benefit from selling?
A key judgement you may have to make in this process is whether a machine should be replaced, or if it’s worth maintaining. This is especially true with older equipment. For example, if a machine has a market value of $30,000 and it will cost $20,000 in maintenance and repairs to keep it running for a few years, you might consider selling it or trading it in for something newer. Another common example is when a machine needs mechanical upgrades that might make sense to invest in, but when you address the old controls, that added cost may not be worth it.
These are financial decisions that challenge fabricators everywhere, but we can help! We can recommend some great options to ensure you are confident you’re making the right choice for your business.
Check out your team
The next step is taking a look at your staff. After all, your machines are nothing without their operator and/or setup man, and a preventative maintenance plan won’t execute itself. Consider whether your team is trained and qualified to perform routine maintenance on your current equipment, and any new machines you plan on introducing to the shop. You’ll want to make sure you have the coverage your facility needs to keep the shop running at optimal capacity – even with potential unplanned employee absences. If not, think about cross-training your current employees or hire new ones to fill any gaps.
Now you’re ready to plan!
This asset auditing process works for any capital equipment. Once you have a full understanding of the assets in your shop and what you need to reach your goals this year, you can devise a plan of action. Create and document your maintenance process, and make sure the team is on board and accountable. Continue to audit your processes and optimize along the way until you have something that works for your shop.
Assessing and auditing your assets early on, and building a solid preventative maintenance plan, will help you mitigate the risk of costly repairs or breakdowns, and allow your shop to be as productive as possible. Plus, it will set you up for more accurate forecasting and capacity planning for years to come – any business owner’s dream!
Comments
Add Comment