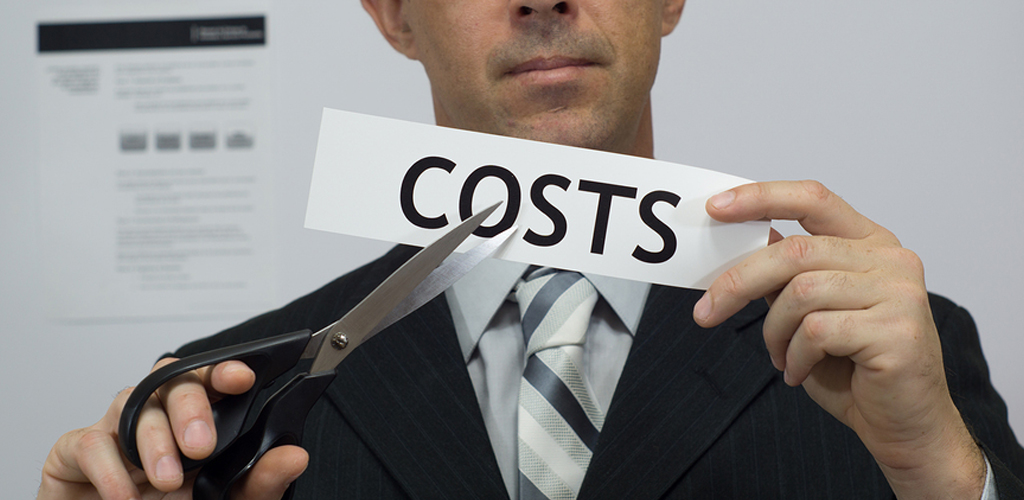
We are all looking to improve efficiencies and increase productivity on the metal fabrication shop floor. After all boosting productivity can mean great things for your business’s bottom line. We get even more excited when boosting productivity and lowering operating costs happen at the same time!
We have already talked about how fiber lasers cut down on processing times with faster piercing and cutting speeds, greater accuracy, and more power for thin to mid-range materials. In comparison to C02 lasers fiber lasers are also better suited for cutting reflective or non-ferrous metals like brass and copper. Although fibre laser purchase costs are comparable to C02 they are 200% more efficient which means greater productivity and more parts per hour (and more dollars in the bank).
Another benefit we can get behind: operating costs can be much less. Many fabricators note that comparably powered solid state resonators are 50% cheaper to operate than C02. Here’s why:
No mirrors, less maintenance
The beam of a fibre laser is delivered by fiber-optic cable. No mirrors are required in the beam path to get the power to the head. The amplified light is then focused by a lens onto the material. This greatly reduces cooling needs as well as optics maintenance especially when it comes to cleaning. While we know machine maintenance is an important part of any metal fabrication business the less maintenance necessary the better. Fiber lasers require 50% lower servicing costs, and machines can run 50% longer between servicing. Machines running smoothly, with minimal time spent on upkeep, results in more time cutting parts.
Solid state keeps it simple
With solid state resonators light creation is simpler and more efficient. These resonators are less complex with fewer moving parts. They don’t require high-priced mechanical components like the turbo blower and vacuum pump which are expensive to replace. This results in dramatically lower operating and maintenance costs.
More power for less power
Another reason fiber lasers have considerably lower operating costs: they have higher electrical efficiency. Solid state resonators consume less electricity for the same output boasting up to 30% wall-plug efficiency with high beam quality. They use far less power than C02 lasers. For example, on average, a 3 kW fiber laser performs using just one third of the power of a 4 kW CO2 machine.
Furthermore solid state resonators can “hibernate” when not in use and will power up immediately when needed. This further reduces power consumption in comparison to C02 machines that need to be constantly on or risk wasting significant time powering up. Less energy consumed means lower operating costs and a happier fabricator.
While C02 machines can be effective for cutting thick materials there is no doubt that fiber lasers come with a host of benefits when it comes to thinner metals – including operating-cost savings. For fabrication shops that mostly handle materials 10mm or less the advantages are clear and as simple as the machines themselves: higher efficiency, increased productivity, and lower costs. What’s in your shop?
Comments
Add Comment