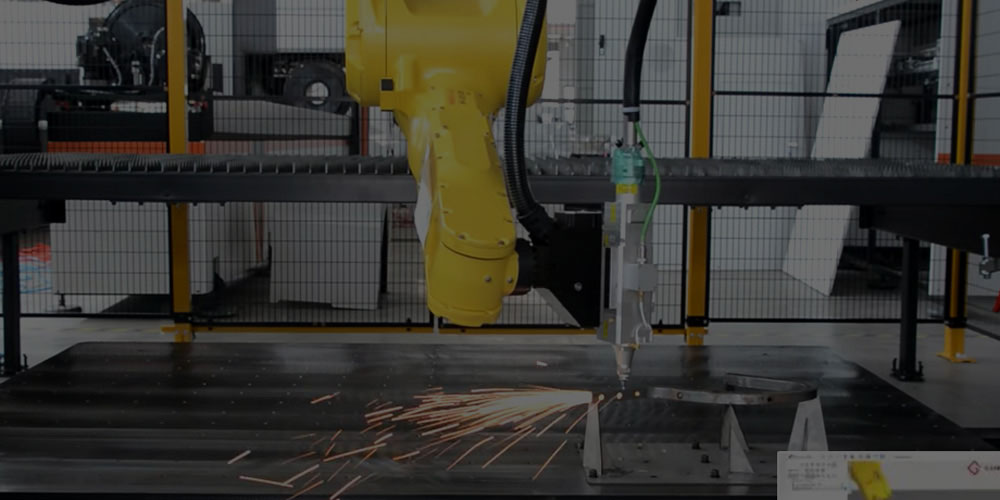
The art of 5 and 6-axis machining in metal fabrication has evolved over recent years. Using a CNC machine tool to cut along 5 or 6 axes simultaneously enables the machining of complex parts for varying applications. Defining coordinates in 3D and communicating multiple, synchronized actions is no easy feat. That said, advancements in machine tool technology and software have come a long way to increase productivity in 5 and 6-axis machining.
As with all CNC operations, a multi-axis machine tool achieves nothing without a program (typically created with CAM software) The complex part geometry of most solid models necessitates CAM software to program the tool paths. Innovations in the CAM space have made machine programming much easier. It all comes down to choosing the right product.
It is practically impossible to manually program 3D cutting. You need CAM software to:
- Visualize your part
- Calculate coordinates across multiple axes, and;
- Communicate with your cutting tool to load new part programs
The good news is, there have been amazing advancements in CAM technology allowing much smoother, more accurate and faster machining in 3D.
When choosing a CAM software for 5 or 6-axis cutting, here’s what to look for:
Does it interact with the machine tools and robots in your shop?
This is the obvious first step; make sure your CAM software works with your equipment.
Products like almaCAM Space Cut are great because they can program any type of 3D-cutting machine or robot. This solution supports all cutting processes from laser and plasma to waterjet and routing.
Does it allow importing solid models or 3D CAD files?
All part designs start with “solid” models from such applications as SolidWorks, Pro/E, Catia, or Inventor. Ensure your CAM solution can work with whatever file type you generate internally or that your customers supply you with in its native format.
Will it provide accurate simulations?
As an operator, you’ll want to visualize what the machine tool is going to do and ensure it can operate within its travel limit or work envelope.
Some of the most prominent advantages to almaCAM Space Cut are the realistic simulations of the cutting sequence and automatic control functions. Plus, display features help visualize possible anomalies. This allows you to easily visualize and validate NC programs.
Is it smart enough to generate automatic collision-free trajectories?
Historically, CNC programming has been a significant barrier to effective and efficient 5 and 6-axis cutting due to the complexities of the process, especially when it comes to avoiding collisions.
Backed by a 40-year history in CAD/CAM technology, almaCAM Space Cut automates the creation of cutting trajectories, using a powerful algorithm to optimize paths, while avoiding collisions. These advanced functions also help reduce programming cycle and cycle times.
Is it user-friendly?
Simplicity is key. Look for a simple and intuitive user interface. Is the control panel easy to read? Does it have clear display of cell objects, cutting profiles, and tree structure views? Check out the import process and ease of object handling. Make sure you can easily modify cutting trajectories.
At the end of the day, you and your crew need to make the software work for you. Alma’s flexible application can be tailored to your unique requirements and processes.
Comments
Add Comment